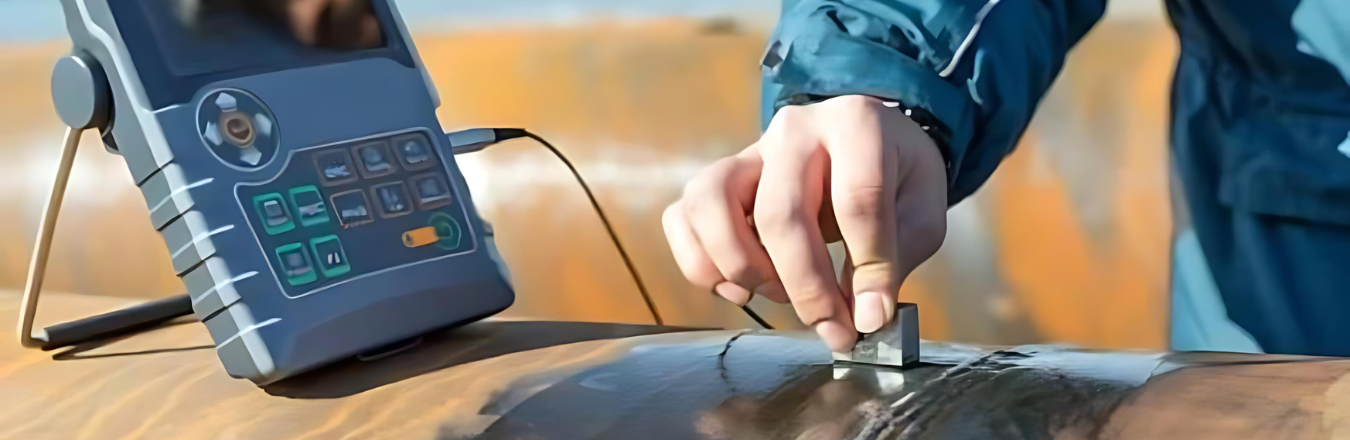
Ultrasonic Testing (UT) uses high frequency sound energy to conduct examinations and make measurements. Ultrasonic inspection can be used for flaw detection/evaluation, dimensional measurements, material characterization, and more.
Ultrasonic testing is carried out using an ultrasonic flaw detector and an ultrasonic probe. In the inspection, ultrasound is sent into the area of interest.
The ultrasound canbe reflected from an interface (ex.Discontinuity) and received by the probe. The reflected ultrasound is displayed on a cathode ray tube screen in the flaw detector and the signal can be analyzed.
This method of inspection is normally carried out on butt welds and is usually limited to section thickness of 8mm and above. It is technically difficult to perform the inspection on thin materials(Less than 12mm) using conventional ultrasonic equipment.
This method is good for detecting internal discontinuities. Surface or near surface discontinuities may not be easily detected.
Here’s a detailed look at various applications of ultrasonic testing:
a) Flaw Detection – Plates, Forgings, Casting & Welding
Ultrasonic testing is widely used to detect internal and surface flaws in various materials and structures:
- Plates: UT helps in identifying laminations, inclusions, and other internal defects.
- Forgings: Detects cracks, voids, and inclusions that could compromise structural integrity.
- Casting: Identifies porosity, inclusions, and cracks that occur during the casting process.
- Welding: Checks for weld defects such as cracks, incomplete fusion, and porosity.
b) Thickness Measurement
UT is a highly effective method for measuring the thickness of materials:
- Corrosion Monitoring: Measures remaining wall thickness in pipes and tanks to detect thinning due to corrosion.
- Structural Integrity: Ensures that materials meet the required thickness specifications to maintain structural integrity.
c) UT Flaw Recording Facility
Ultrasonic testing systems often come equipped with recording facilities that provide:
- Digital Storage: Recorded A-scan, B-scan, and C-scan data for future reference and analysis.
- Documentation: Detailed reports including flaw type, size, and location.
- Traceability: Maintains records that are crucial for quality control and regulatory compliance.
d) Corrosion Mapping with B Scan
B-scan is a method used to visualize the cross-sectional profile of a material:
- Corrosion Mapping: Provides a detailed image of the internal structure, showing areas of corrosion or thinning.
- Maintenance Planning: Helps in planning maintenance by identifying areas needing immediate attention.
e) USFD Test of Rail AT and FB Weld Joints
Ultrasonic Flaw Detection (USFD) is crucial for ensuring the safety and reliability of railways:
- Rail Joints: AT (Aluminothermic) and FB (Flash Butt) weld joints in rails are inspected for cracks and inclusions.
- Safety: Ensures that rail welds meet stringent safety standards to prevent accidents and derailments.